Master Inventory Management: The Ultimate Guide to Setting It Up in ERPNext
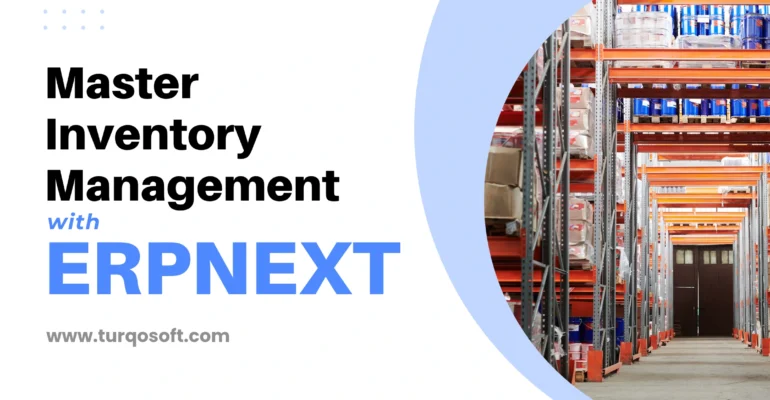
Managing inventory efficiently is crucial for businesses aiming to balance supply and demand while minimizing costs. If you’re using ERPNext, you’re already a step ahead in leveraging technology for seamless inventory operations. However, setting up inventory management in ERPNext can seem overwhelming if you’re new to the platform.
In this guide, we’ll walk you through the entire process—from configuration to execution. By the end, you’ll be equipped to handle inventory like a pro and scale your business with confidence.
1. Why ERPNext for Inventory Management?
ERPNext stands out as one of the most versatile open-source ERP platforms, offering robust inventory management features tailored to meet the needs of various industries.
Key Benefits:
- Real-Time Stock Updates: Track inventory levels across multiple warehouses in real time.
- Multi-Warehouse Management: Manage complex supply chains with ease.
- Integration with Other Modules: Seamlessly connect inventory with sales, purchase, and manufacturing modules.
- Customization Options: Tailor inventory workflows to suit your specific business needs.
By choosing ERPNext, you’re opting for an affordable, scalable, and user-friendly solution to streamline inventory processes.
2. Pre-Requisites for Setting Up Inventory
Before diving into the setup, ensure the following are in place:
- ERPNext Instance: Make sure your ERPNext system is up and running.
- Basic Data: Gather essential data such as product details, stock levels, and supplier information.
- Warehouse Structure: Decide how your warehouses will be organized in ERPNext.
- User Permissions: Define roles and access levels for users managing inventory.
Proper preparation ensures a smooth and error-free setup.
3. Step-by-Step Guide to Setting Up Inventory in ERPNext
Step 1: Configure Item Master
The Item Master is the heart of inventory management in ERPNext. Here’s how to set it up:
- Go to Items > New Item.
- Enter basic details such as Item Code, Item Name, and Item Group.
- Define item types: Stock, Non-Stock, or Service.
- Set default units of measure (e.g., pcs, kg).
- Configure additional parameters like reorder levels, batch tracking, and serial numbers.
Step 2: Set Up Warehouses
Warehouses help in organizing inventory.
- Navigate to Stock > Warehouses > Create New Warehouse.
- Assign a Warehouse Code and Parent Warehouse (if applicable).
- Specify the location and any other relevant details.
- Save your warehouse structure.
Step 3: Input Opening Stock Balances
For accurate tracking, input your current inventory.
- Go to Stock > Stock Entry > New Stock Entry.
- Choose Purpose: Opening Stock.
- Select the items and input their quantities.
- Save and Submit the entry.
Step 4: Configure Stock Settings
Fine-tune your inventory management settings:
- Navigate to Stock Settings under the Stock Module.
- Enable features such as “Manage Serial Numbers,” “Manage Batches,” or “Auto Material Request.”
- Define valuation methods (FIFO, Moving Average, etc.).
- Save the settings.
Step 5: Link Inventory with Other Modules
- Sales Module: Ensure items are linked to sales invoices and orders.
- Purchase Module: Sync items with purchase orders for seamless restocking.
- Manufacturing Module: Connect raw materials to finished goods for BOM tracking.
Step 6: Automate Reordering
Set reorder levels for critical items to prevent stockouts.
- Go to Item > Reorder Level.
- Define reorder thresholds and preferred suppliers.
- Enable automatic Material Request generation.
Step 7: Test Your Setup
Perform a test run by creating stock entries, purchase orders, and sales invoices to ensure everything functions as intended.
4. Common Pitfalls and How to Avoid Them
- Incorrect Data Entry: Double-check all item details before saving.
- Lack of Training: Train your team to prevent errors in day-to-day operations.
- Ignoring Updates: Regularly update ERPNext to access new features and security patches.
5. Advanced Inventory Features to Explore
Once you’ve mastered the basics, take advantage of these advanced features:
- Batch and Serial Number Tracking: Ideal for industries like pharmaceuticals and electronics.
- Multi-Warehouse Transfers: Optimize stock movement between locations.
- Landed Cost Voucher: Accurately account for additional costs like shipping.
- Stock Aging Reports: Analyze inventory turnover to identify slow-moving items.
6. Tips for Maximizing Inventory Efficiency
- Regular Audits: Perform physical stock audits to ensure system accuracy.
- ABC Analysis: Prioritize high-value items to optimize inventory investment.
- Forecasting: Use historical data to predict demand and avoid overstocking.
- Integration with E-Commerce: Sync your inventory with online stores for real-time updates.
7. Conclusion
Setting up inventory management in ERPNext is a transformative step for your business. By following this guide, you can streamline operations, reduce costs, and enhance customer satisfaction.
If you’re seeking expert guidance for the seamless implementation and customization of ERPNext, unlocking its full potential for your organization, look no further. Reach out to us, and our seasoned team will be thrilled to provide the assistance you need.
Feel free to drop us a message, either via email at info@turqosoft.com or by giving us a call at +91 9841205845.
Alternatively, stay connected with us on various social media platforms such as LinkedIn, YouTube, Facebook, Twitter, Pinterest, or Instagram to receive regular updates on ERPNext and other pertinent topics.
Image Credit: Canva